FUEL PUMP OPERATION 1. Install Jumper Wire (SST-09843-18020) between +B and FP terminals of data link connector. See Fig. 1 . The data link connector is located in engine compartment. 2. On all models, turn ignition on. Listen for fuel pump operating sound and feel for pressure in fuel line near fuel filter. Turn ignition off. Remove jumper wire. If fuel pump operates, check fuel pressure. See FUEL PRESSURE . 3. If fuel pump does not operate, connect a jumper wire from battery source to FP terminal of data link connector. If fuel pump operates, EFI main relay, EFI No. 2 relay, circuit opening relay or fuel pump relay may be defective. For explanation of relay operation, see FUEL PUMP CONTROL CIRCUIT . 4. If relays are okay, check wiring circuit and fuses. If fuel pump does not operate, check for defective fuel pump, open circuit between data link connector and fuel pump, or defective fuel pump ground or fuses. See appropriate wiring diagram in the WIRING DIAGRAMS article. Fig. 1: Installing Jumper Wire In DLC Courtesy of TOYOTA MOTOR SALES, U.S.A., INC FUEL PRESSURE 1. Ensure battery is fully charged and ignition is off. Disconnect negative battery cable. Disconnect electrical connector from cold start injector (if equipped). 2. Note location of fuel pressure gauge installation. See Fig. 2 . Place container under cold start injector pipe, deliver pipe or fuel filter. Cover union bolt with shop towel, and slowly loosen union bolt to relieve fuel pressure. 3. Remove union bolt and gaskets. Install Fuel Pressure Gauge (SST 09268-45012) using NEW gaskets. See Fig. 2 . Tighten union bolt. Reconnect negative battery cable. 4. Install jumper wire between +B and FP terminals of data link connector. See Fig. 1 . The data link connector is located in engine compartment. 5. Turn ignition on and note fuel pressure. Fuel pressure should be within specification. See FUEL PUMP PERFORMANCE table. 6. If fuel pressure exceeds specification, replace fuel pressure regulator. If fuel pressure is less than specified, check for defective fuel lines, connections, fuel pump, fuel filter or fuel pressure regulator. 7. Remove jumper wire from data link connector. Start engine and allow to idle. Disconnect and plug vacuum line at fuel pressure regulator. Note fuel pressure. 8. Reconnect vacuum hose on fuel pressure regulator, and note fuel pressure. Fuel pressure should be within specification. See the FUEL PRESSURE SPECIFICATIONS table. 9. If fuel pressure is not within specification, check for defective vacuum hose or fuel pressure regulator. Shut engine off and note fuel pressure. 10. Fuel pressure should hold at least 21 psi (1.5 kg/cm 2 ) for a minimum of 5 minutes. If fuel pressure does not hold as specified, check for defective fuel pump, fuel injector or fuel pressure NOTE: All models use in-tank fuel pump. Fuel pump contains internal relief valve and check valve.regulator. 11. Disconnect negative battery cable. Remove fuel pressure gauge. Reinstall union bolt using NEW gaskets. Tighten union bolt. Install cold start injector electrical connector (if equipped). Install negative battery cable. NOTE: For more information on checking fuel injectors and other fuel sub- systems, see SYSTEM/COMPONENT TESTS article.
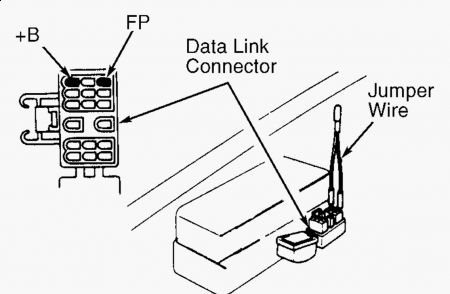
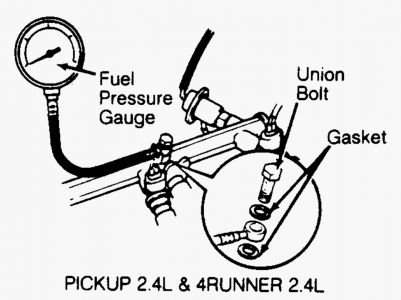
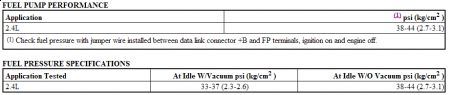
FUEL PUMP CONTROL CIRCUIT EFI Main Relay The EFI fuse supplies constant battery voltage to EFI main relay. The EFI main relay provides battery voltage to +B terminal of circuit opening relay (some models) and data link connector. Depending on model, EFI main relay may either be turned on directly by ignition switch or by M- REL terminal of Engine Control Module (ECM). The EFI main relay may also provide battery voltage to +B and +B1 terminals of ECM when ignition is turned on. The EFI main relay is located in engine compartment relay box. Circuit Opening Relay Circuit opening relay controls fuel pump circuit. The Engine Control Module (ECM) receives an input signal at STA terminal when engine is cranking. Starter signal is also applied to STA terminal of circuit opening relay. Starter signal energizes circuit opening relay during cranking. Circuit opening relay then provides voltage to fuel pump or fuel pump relay. The fuel pump switch in the airflow meter provides ground for circuit opening relay. NOTE: For information on testing relays and fuel system components, see the SYSTEM/COMPONENT TESTS article. Relays may be identified by appropriate illustration in the THEORY/OPERATION article. NOTE: Circuit opening relay is used on all models.
COLD START INJECTOR TIME SWITCH 1. Ensure ignition is off. Disconnect electrical connector from cold start injector time switch. 2. Cold start injector time switch is located in engine coolant passage near cylinder head or thermostat housing. To verify wire colors for proper identification, see appropriate wiring diagram in WIRING DIAGRAMS article in the ENGINE PERFORMANCE section. 3. Note cold start injector time switch terminal identification. See Fig. 3 . Using ohmmeter, measure resistance at designated switch terminals at specified temperature. See COLD START INJECTOR TIME SWITCH RESISTANCE SPECIFICATIONS table. Replace cold start injector time switch if resistance is not within specification. COLD START INJECTOR TIME SWITCH RESISTANCE SPECIFICATIONS NOTE: Cold start injector time switch may also be identified using appropriate illustration in THEORY/OPERATION article in the ENGINE PERFORMANCE section.
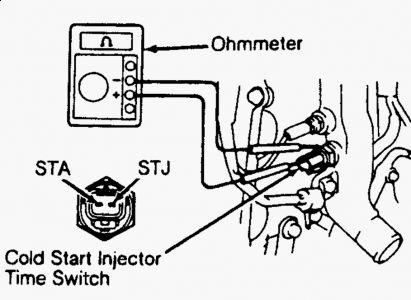
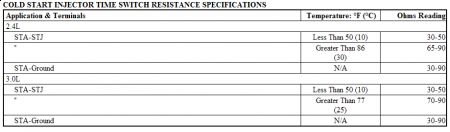
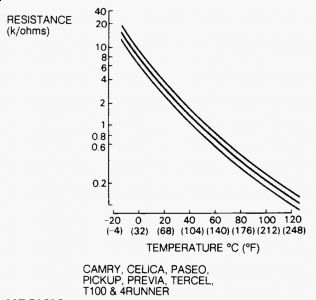
COOLANT TEMPERATURE SENSOR (CTS) 1. Ensure ignition is off. Disconnect electrical connector from CTS. CTS is located in engine coolant passage near cylinder head or thermostat housing. To verify wire colors for proper identification, see appropriate wiring diagram in WIRING DIAGRAMS article in the ENGINE PERFORMANCE section. 2. Using ohmmeter, check resistance between CTS electrical terminals. Resistance should be within specification at designated temperature. See Fig. 4 . Replace CTS if resistance is not within specification. NOTE: The CTS may be also identified using appropriate illustration in THEORY/OPERATION article in the ENGINE PERFORMANCE section.
Cold Start Injector 1. Disconnect negative battery cable. Disconnect cold start injector wiring harness connector. 2. Using ohmmeter, measure resistance between electrical terminals of cold start injector. Replace cold start injector if resistance is not 2-4 ohms. Remove cold start injector. See N - REMOVE/INSTALL/OHAUL article in the ENGINE PERFORMANCE section. 3. On all models except Pickup 3.0L, install Union Adapters (SST 09268-41045) with NEW gaskets on cold start injector and delivery pipe. Connect delivery hose to union adapters. See Fig. 24 . 4. On Pickup 3.0L, install cold start injector or delivery hose with union bolt and NEW gaskets on cold start injector. 5. On all models, reconnect negative battery cable. Connect Jumper Wire (SST 09843-18020) between terminals FP and +B of data link connector No. 1. Turn ignition on, with engine off to pressurize fuel system. 6. Place tip of cold start injector in a container. Connect cold start injector tester to cold start injector. Use Cold Start Injector Tester (SST 09842-30050). 7. Connect cold start injector tester to battery. See Fig. 24 and Fig. 25 . Ensure fuel spray pattern is an even cone shape. Disconnect cold start injector tester from battery. 8. Check for fuel leakage from cold start injector. Maximum leakage should be one drop per minute with fuel pressure applied. Replace cold start injector if defective. Disconnect negative battery cable and test equipment. NOTE: For proper location of data link connector No. 1 and terminal identification, see BASIC TESTING article in the ENGINE PERFORMANCE section. Jumper wire is installed in data link connector No. 1 when checking fuel pump operation and fuel pressure. CAUTION: Perform cold start injector test in shortest possible time to check fuel spray pattern. NOTE: Cold start injector is controlled by cold start injector time switch when ignition is turned on.
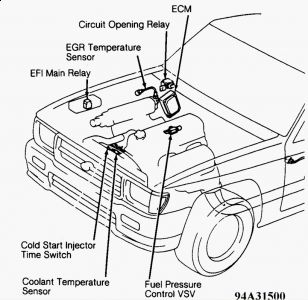
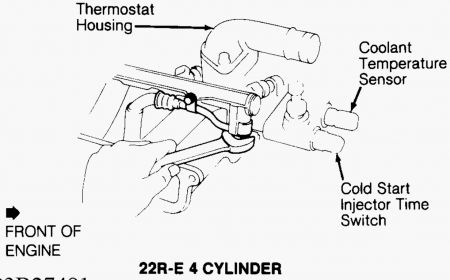
Tuesday, October 16th, 2018 AT 1:19 PM
(Merged)