Running Loss With On-Board Refueling Vapor Recovery (ORVR) System
This system allows vapor generated during refueling to be collected by charcoal canisters. System uses 2 charcoal canisters connected in series to reduce hydrocarbon emissions. A tank pressure sensor and canister close valve are used by the on-board diagnostic system to test for leaks in the system. See Fig. 12 . During normal running, vapor is collected and purged in the same manner as the Running Loss System.
The ORVR system has the following features:
A narrow fuel filler pipe providing a liquid seal when refueling, which prevents fuel vapor from venting to the atmosphere.
There is no vent between the tank and the filler pipe. A check valve at the lower end of the filler pipe is used to prevent fuel from surging up the filler pipe while refueling.
A Fuel Level Vent Valve (FLVV) consisting of a 2-stage shut-off valve with rollover protection and a pressure relief valve.
A grade vent valve with rollover protection and an outlet pipe connected to the FLVV outlet pipe.
Larger bore vapor pipes.
During refueling, the tank is vented through the FLVV, vapor hoses and charcoal canisters. The FLVV incorporates a float valve which is closed by the rising fuel level, creating a backpressure and causing refueling to stop. When the FLVV is closed (tank is full), any increase in pressure is relieved by the grade vent valve, by-passing the FLVV. When the FLVV is open, vapor vents to the canisters normally. The pressure relief valve allows vapor venting through the filler cap if a blockage or failure occurs.
Fig. 12: Identifying Running Loss With ORVR System Components
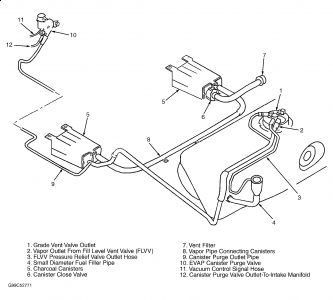
SPONSORED LINKS
Thursday, December 31st, 2009 AT 8:25 PM