Hello -
Okay, here is what I have done. I first gave you all the info I have on troubleshooting the cruise control system.
I know I gave you more troubleshooting than what your problem is, but I figured while your mechanic is troubleshooting he may get into another area and not have it. So, I figured it is better to have too much info than not enough.
I attached the two Figures it refers to at the end.
You will have to copy paste and then blow up a little the wiring diagram. I split them so they would be bigger so you will have to tape them together. If they are still too small let me know and I will try something else.
DESCRIPTION & OPERATION
Major components of the cruise control system are speed control switches, servo/actuator, vehicle speed sensor, Brake Pedal Position (BPP) switch, deactivator switch, Clutch Pedal Position (CPP) switch, and related wiring. This system does not require engine vacuum. An electronic servo/actuator actuates the throttle. All electronic control components are contained within the servo/actuator assembly.
The system is operational only at speeds greater than 30 MPH. The system is activated when ON/OFF switch is switched on and SET/ACCEL button is pressed and released. Vehicle will maintain set speed until new speed is set, brake pedal is pressed, clutch pedal is pressed, or ON/OFF switch is switched off. If system has been deactivated by pressing brake pedal or clutch pedal, set speed can be regained by pressing and releasing RESUME button. When brake pedal or clutch pedal is pressed, a signal from switch is sent to the servo to deactivate the system. A deactivator switch acts as a redundant brake signal.
ADJUSTMENTS
SERVO/ACTUATOR CABLE
NOTE: The speed control servo/actuator cable is not adjustable on vehicles equipped with ZETEC engine. Cable adjustment is for vehicles equipped with 2.0 L SPI engine only.
Disconnect speed control servo/actuator cable from throttle control lever. Remove speed control servo/actuator cable adjuster clip from cable adjuster. Ensure throttle is fully closed. Adjust speed control servo/actuator cable until freeplay is .04-.12" (1-3 mm). Install speed control servo/actuator cable adjuster clip. Ensure throttle linkage operates freely and smoothly.
SYSTEM TESTING
TEST A: SPEED CONTROL IS INOPERATIVE
1. Check For Power & Ground To Speed Control Servo/Actuator - Turn ignition off. Disconnect speed control servo/actuator connector C177 (located on left front side of engine compartment). Turn ignition switch to RUN position. Using a voltmeter, check voltage between speed control servo/actuator connector C177 terminals No. 7 and 10. See Fig. 1 . If voltage is more than 10 volts, go to step 4). If voltage is 10 volts or less, go to next step.
2. Check Fuse - Turn ignition off. Check instrument panel fuse block fuse No. 1 (10-amp). If fuse is okay, go to next step. If fuse is not okay, replace fuse and retest system operation. If fuse fails again, check for short to ground in Yellow wire between instrument panel fuse block and speed control servo/actuator. Repair as necessary and retest system operation.
3. Check Speed Control Servo/Actuator Ground Circuit - Using an ohmmeter, check resistance between ground and speed control servo/actuator connector C177 terminal No. 10. See Fig. 1 . If resistance is less than 5 ohms, repair open in Yellow wire between instrument panel fuse block and speed control servo/actuator. Retest system operation. If resistance is 5 ohms or more, repair open in Blue wire between speed control servo/actuator and ground.
4. Check Stoplight Operation - Check stoplight operation while pressing brake pedal. If stoplights operate properly, go to next step. If stoplights do not operate properly, see appropriate EXTERIOR LIGHTS wiring diagram in SYSTEM WIRING DIAGRAMS article in the WIRING DIAGRAMS section to continue diagnosis.
5. Check Brake Circuit - Using an ohmmeter, check resistance between speed control servo/actuator connector C177 terminals No. 4 and 10. If resistance is less than 20 ohms, go to step 8). If resistance is 20 ohms or more and vehicle is equipped with M/T, go to next step. If resistance is 20 ohms or more and vehicle is equipped with A/T, repair Green wire between speed control servo/actuator and Brake Pedal Position (BPP) switch. Retest system operation.
6. Check Clutch Pedal Position (CPP) Switch - Ensure ignition is off. Disconnect CPP switch connector C292 (located on top of clutch pedal support). Using an ohmmeter, check resistance between CPP switch terminals (switch side). If resistance is less than 5 ohms, go to next step. If resistance is 5 ohms or more, replace CPP switch and retest system operation.
7. Check Green Wire For Open - Ensure ignition is off. Disconnect BPP switch connector C245 (located on top of brake pedal support). Using an ohmmeter, check resistance in Green wire between CPP switch connector C292 and BPP switch connector C245. If resistance is less than 5 ohms, repair White or Green wire between speed control servo/actuator and CPP switch. Retest system operation. If resistance is 5 ohms or more, repair open in Green wire between CPP switch and BPP switch. Retest system operation.
8. Check Deactivator Switch Input To Speed Control Servo/Actuator - Ensure ignition is off. Using a voltmeter, check voltage between speed control servo/actuator connector C177 terminals No. 9 and 10. See Fig. 1 . If voltage is 10 volts or less, go to next step. If voltage is more than 10 volts, go to step 11).
9. Check Deactivator Switch - Ensure ignition is off. Disconnect deactivator switch connector C208 (located on top of brake pedal support). Using an ohmmeter, check resistance between deactivator switch terminals (switch side). If resistance is less than 5 ohms, go to next step. If resistance is 5 ohms or more, replace deactivator switch and retest system operation.
10. Check For Power To Deactivator Switch - Using a voltmeter, check voltage between ground and deactivator switch connector C208 Green/White wire terminal. If voltage is more than 10 volts, repair Green/Yellow wire between deactivator switch and speed control servo/actuator. Retest system operation. If voltage is 10 volts or less, repair Green/White wire between instrument panel fuse block and deactivator switch. Retest system operation.
11. Check Red/Yellow Wire For Short To Power - Ensure ignition is off. Using a voltmeter, check voltage between speed control servo/actuator connector C177 terminals No. 5 and 10. See Fig. 1 . If voltage is indicated, go to next step. If no voltage is indicated, go to step 14).
12. Check For Stuck Speed Control Switch - Disconnect speed control switch connector C269 (located in steering wheel, under air bag module). Turn ignition switch to RUN position. Using a voltmeter, check voltage between speed control servo/actuator connector C177 terminals No. 5 and 10. See Fig. 1 . If voltage is indicated, go to next step. If no voltage is indicated, replace speed control switches and retest system operation.
13. Check Red/Yellow Wire For Short To Power - Ensure ignition is off. Disconnect air bag sliding contact connector C248 (located under steering wheel). Turn ignition to RUN position. Using a voltmeter, check voltage between speed control servo/actuator connector C177 terminals No. 5 and 10. See Fig. 1 . If voltage is indicated, repair short to power in Red/Yellow wire between air bag sliding contact and speed control servo/actuator. Retest system operation. If no voltage is indicated, replace air bag sliding contact and retest system operation.
14. Check Speed Control Switch SET/ACCEL Operation - Using an ohmmeter, check resistance between speed control servo/actuator connector C177 terminals No. 5 and 6 while pressing speed control SET/ACCEL switch. If resistance is 640-720 ohms, go to next step. If resistance is not 640-720 ohms, go to step 16).
15. Check Speed Control Switch ON Operation - Turn ignition switch to RUN position. Using a voltmeter, check voltage between speed control servo/actuator connector C177 terminals No. 5 and 6 while pressing speed control ON switch. If voltage is more than 10 volts, go to step 19). If voltage is 10 volts or less, replace speed control switch and retest system operation.
16. Check Red/Yellow Wire For Open - Ensure ignition is off. Disconnect air bag sliding contact connector C248 (located under steering wheel). Using an ohmmeter, check resistance in Red/Yellow wire between air bag sliding contact connector C248 (male side) and speed control servo/actuator connector C177 terminal No. 5. If resistance is less than 5 ohms, go to next step. If resistance is 5 ohms or more, repair open in Red/Yellow wire and retest system operation.
17. Check Red/Blue Wire For Open - Using an ohmmeter, check resistance in Red/Blue wire between air bag sliding contact connector C248 (male side) and speed control servo/actuator connector C177 terminal No. 6. If resistance is less than 5 ohms, go to next step. If resistance is 5 ohms or more, repair open in Red/Blue wire and retest system operation.
18. Check Air Bag Sliding Contact - Disconnect speed control switch connector C269 (located in steering wheel, under air bag module). Using an ohmmeter, check resistance between speed control switch connector C269 (female side) terminals No. 1 and 2 while pressing speed control SET/ACCEL switch. See Fig. 2 . If resistance is 640-720 ohms, replace air bag sliding contact and retest system operation. If resistance is not 640-720 ohms, replace speed control switch and retest system operation.
19. Check Speedometer Operation - Test drive vehicle and observe speedometer operation. If speedometer operates properly, go to next step. If speedometer does not operate properly, see appropriate INSTRUMENT PANELS article to continue diagnosis.
20. Check Speed Control Servo/Actuator Cable & Throttle Body Linkage - Ensure ignition is off. Remove speed control servo/actuator cable from speed control servo/actuator. Inspect cable by pulling end of cable and observing throttle movement. Replace cable if broken or binding. Retest system operation. If cable is okay, replace servo/actuator and retest system operation.
Fig. 1: Speed Control Servo/Actuator Connector
C177 Terminals
Courtesy of FORD MOTOR CO.
Fig. 2: Speed Control Switch Connector C269 Terminals
Courtesy of FORD MOTOR CO.
TEST B: SET SPEED FLUCTUATES
1. Check Speed Control Servo/Actuator Cable & Throttle Body Linkage - Ensure ignition is off. Disengage speed control servo/actuator cable from from servo/actuator. Inspect cable by pulling end of cable and observing throttle movement. If cable is okay, go to next step. Replace cable if broken or binding and retest system operation. Repair throttle body linkage if necessary, and retest system operation.
2. Check Speedometer Operation - Drive vehicle and observe speedometer operation without using speed control. If speedometer needle fluctuates, see appropriate INSTRUMENT PANELS article to continue diagnosis. If speedometer needle does not fluctuate, replace speed control servo/actuator and retest system operation.
TEST C: SPEED CONTROL DOES NOT DISENGAGE WHEN BRAKES ARE
APPLIED
1. Check Stoplight Operation - Press brake pedal and observe stoplight operation. If stoplights operate properly, go to next step. If stoplights do not operate properly, see appropriate wiring diagram in EXTERIOR LIGHTS article to continue diagnosis.
2. Check Brake Circuit - Ensure ignition is off. Disconnect speed control servo/actuator connector C177 (located on left front side of engine compartment). Using an ohmmeter, check resistance between speed control servo/actuator connector C177 terminals No. 4 and 10. See Fig. 1 . If resistance is less than 20 ohms, replace speed control servo /actuator and retest system operation. If resistance is 20 ohms or more and vehicle is equipped with M/T, go to next step. If resistance is 20 ohms or more and vehicle is equipped with A/T, repair Green wire between speed control servo/actuator and BPP switch. Retest system operation.
3. Check Clutch Pedal Position (CPP) Switch - Ensure ignition is off. Disconnect CPP switch connector C292 (located on top of clutch pedal support). Using an ohmmeter, check resistance between CPP switch terminals (switch side). If resistance is less than 5 ohms, go to next step. If resistance is 5 ohms or more, replace CPP switch and retest system operation.
4. Check Green Wire For Open - Ensure ignition is off. Disconnect BPP switch connector C245 (located on top of brake pedal support). Using an ohmmeter, check resistance in Green wire between CPP switch connector C292 and BPP switch connector C245. If resistance is less than 5 ohms, repair White or Green wire between speed control servo/actuator and CPP switch. Retest system operation. If resistance is 5 ohms or more, repair open in Green wire between CPP switch and BPP switch. Retest system operation.
TEST D: SPEED CONTROL DOES NOT DISENGAGE WHEN CLUTCH IS
APPLIED
1. Check Clutch Pedal Position (CPP) Switch - Ensure ignition is off. Disconnect CPP switch connector C292 (located on top of clutch pedal support). Using an ohmmeter, check resistance between CPP switch terminals (switch side) while pressing clutch pedal. If resistance is more than 10 k/ohms, go to next step. If resistance measurement is 10 k/ohms or less, replace CPP switch and retest system operation.
2. Check Green Wire & White Wire For Short To Ground - Ensure ignition is off. Disconnect speed control servo/actuator connector C177 (located on left front side of engine compartment). Using an ohmmeter, check resistance between ground and speed control servo/actuator connector C177 terminal No. 4. See Fig. 1 . If resistance is more than 10 k/ohms, replace speed control servo/actuator and retest system operation. If resistance is 10 k/ohms or less, repair short to ground in Green wire or White wire. Retest system operation.
TEST E: COAST SWITCH IS INOPERATIVE
Check COAST Switch
Ensure ignition is off. Disconnect speed control servo/actuator connector C177 (located on left front side of engine compartment). Using an ohmmeter, check resistance between speed control servo/actuator connector C177 terminals No. 5 and 6 while pressing speed control COAST switch. See Fig.
1 . If resistance is 114-126 ohms, replace speed control servo/actuator and retest system operation. If resistance is not 114-126 ohms, replace speed control switches and retest system operation.
TEST F: SET/ACCL SWITCH IS INOPERATIVE
Check SET/ACCL Switch
Turn ignition off. Disconnect speed control servo/actuator connector C177 (located on left front side of engine compartment). Using an ohmmeter, check resistance between speed control servo/actuator connector C177 terminals No. 5 and 6 while pressing speed control SET/ACCL switch. See Fig. 1 . If resistance is 646-714 ohms, replace speed control servo/actuator and retest system operation. If resistance is not 646-714 ohms, replace speed control switches and retest system operation.
TEST G: RESUME SWITCH IS INOPERATIVE
Check RESUME Switch
Turn ignition off. Disconnect speed control servo/actuator connector C177 (located on left front side of engine compartment). Using an ohmmeter, check resistance between speed control servo/actuator connector C177 terminals No. 5 and 6 while pressing speed control RESUME switch. See Fig. 1 . If resistance is 2090-2310 ohms, replace speed control servo/actuator and retest system operation. If resistance is not 2090-2310 ohms, replace speed control switches and retest system operation.
TEST H: OFF SWITCH IS INOPERATIVE
Check OFF Switch
Turn ignition off. Disconnect speed control servo/actuator connector C177 (located on left front side of engine compartment). Using an ohmmeter, check resistance between speed control servo/actuator connector C177 terminals No. 5 and 6 while pressing speed control OFF switch. See Fig. 1 . If resistance is less than 5 ohms, replace speed control servo/actuator and retest system operation. If resistance is 5 ohms or more, replace speed control switches and retest system operation.
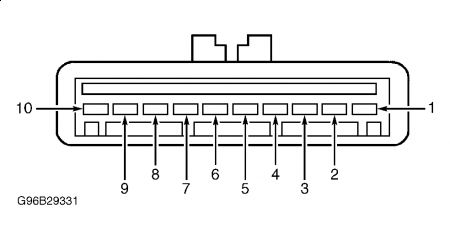
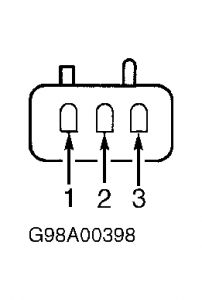
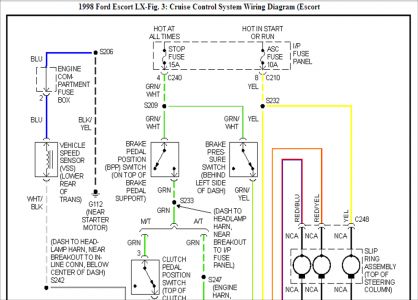
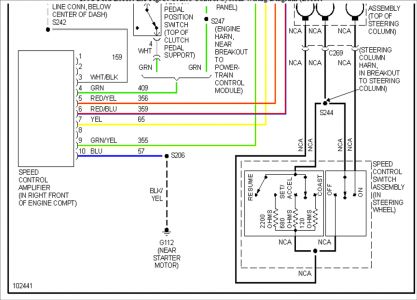
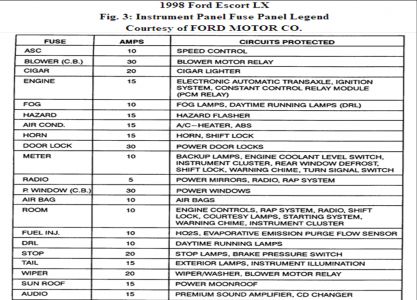
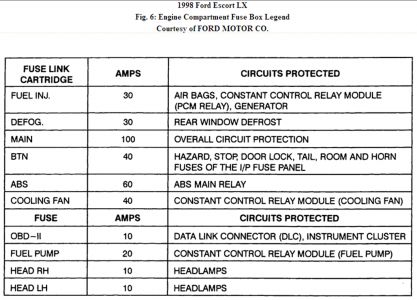
Next I have attached info on the instrument panel. . .. . .figures at the end
DESCRIPTION & OPERATION
WARNING: Deactivate air bag system before performing any service operation. See AIR BAG RESTRAINT SYSTEM article. DO NOT apply electrical power to any component on steering column without first deactivating air bag system. Air bag may deploy.
Instrument cluster contains a speedometer/odometer, tachometer (if equipped), fuel gauge, temperature gauge and various warning lights placed in groups at bottom of instrument cluster. See Fig. 1 and Fig. 2 .
Instrument cluster gauge amplifier is part of low fuel level warning/anti-slosh module and provides delay in fuel gauge to prevent fluctuation in fuel gauge pointer as a result of fuel movement in tank. The module is a small printed circuit board which latches into a pocket on back of instrument cluster. See Fig. 3 . There are no provisions for calibration or adjustment of low fuel level warning/anti-slosh module.
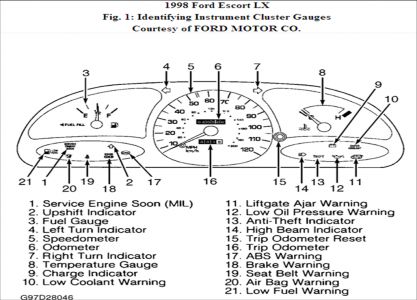
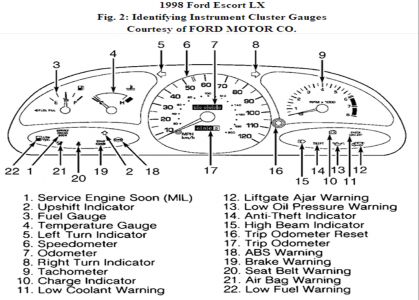
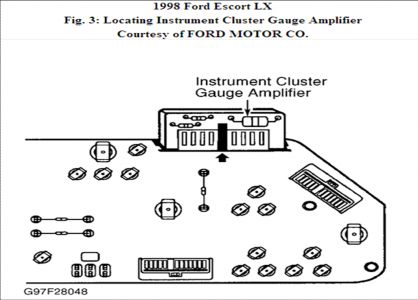
TEST D: SPEEDOMETER/ODOMETER INACCURATE
1. Turn ignition off. Connect scan tool and retrieve Diagnostic Trouble Codes (DTC) following manufacturer's instructions. If no DTCs are present, go to next step. If DTCs are present, see appropriate TESTS W/CODES article in the ENGINE PERFORMANCE section. Repair DTCs as necessary, then retest system.
2. Using scan tool, observe Vehicle Speed Sensor (VSS) output Parameter Identification (PID) while assistant drives vehicle over range of speeds on various road surfaces. If VSS PID varies smoothly with vehicle speed, go to next step. If VSS PID does not vary or is erratic, see appropriate TESTS W/CODES article in the ENGINE PERFORMANCE section to diagnose VSS.
3. Remove and check OBDII 10-amp fuse in engine compartment fuse box. If fuse is okay, reinstall fuse and go to step 5). If fuse is blown, go to next step.
4. Turn ignition off. Remove instrument cluster. See INSTRUMENT CLUSTER under REMOVAL & INSTALLATION. Disconnect instrument cluster electrical connectors. Measure resistance between ground and instrument cluster harness connector C252 terminal No. 12 (Green wire). See Fig. 6 . Measured resistance should be more than 10 k/ohms. If resistance is more than 10 k/ohms, replace OBDII 10-amp fuse and go to next step. If resistance is less than 10 k/ohms, repair Green wire between instrument cluster harness connector and fuse. See WIRING DIAGRAMS.
5. Turn ignition off. Remove instrument cluster. See INSTRUMENT CLUSTER under REMOVAL & INSTALLATION. Disconnect instrument cluster electrical connectors. Measure voltage between ground and instrument cluster harness connector C252 terminal No. 12 (Green wire). See Fig. 6 . Voltage should be more than 10 volts. If voltage is more than 10 volts, go to next step. If voltage is less than 10 volts, repair Green wire between instrument cluster harness connector and fuse. See WIRING DIAGRAMS.
6. Turn ignition off. Disconnect Vehicle Speed Sensor (VSS) harness connector. Measure resistance of Blue wire between VSS harness connector and instrument cluster harness connector C252 terminal No. 7. See Fig. 6 . Measure resistance of White/Black wire between VSS harness connector and instrument cluster harness connector C252 terminal No. 9. Resistance in both tests should be less than 5 ohms. If resistances are as specified, go to next step. If resistances are not as specified, repair wire in question. See WIRING DIAGRAMS.
7. Measure resistance between ground and instrument cluster harness connector C252 terminal No. 9 (White/Black wire). Resistance should be more than 10 k/ohms. If measured resistance is more than 10 k/ohms, go to next step. If resistance is less than 10 k/ohms, repair short in White/Black wire.
8. Turn ignition on. Measure voltage between ground and instrument cluster harness connector C252 terminals No. 8 and 4 (Black/Yellow wire). See Fig. 6 . Voltage should be more than 10 volts. If voltage is more than 10 volts, go to next step. If voltage is less than 10 volts, repair Black/Yellow wire between instrument cluster connector and fuse. See WIRING DIAGRAMS.
9. Turn ignition off. Visually inspect instrument cluster printed circuit for damage, cracks or hot spots. If instrument cluster printed circuit is okay, replace speedometer. If instrument cluster printed circuit is damaged, replace printed circuit and gauge contact clips. See PRINTED CIRCUIT under REMOVAL & INSTALLATION.
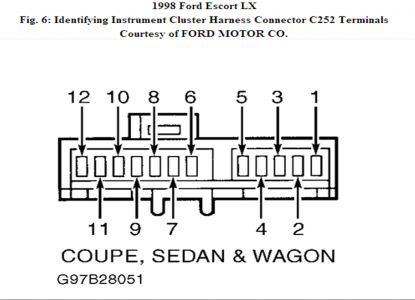
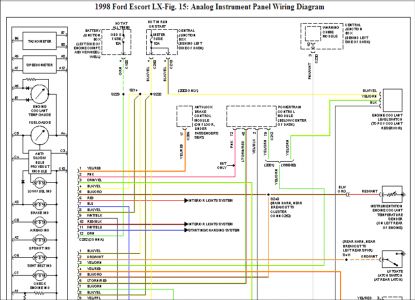
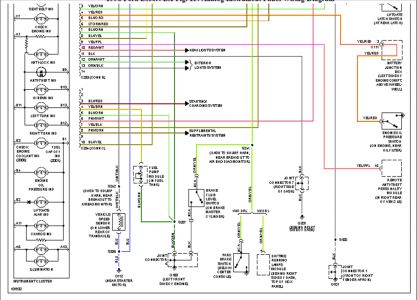
Okay let me know if this works for you
Wednesday, March 25th, 2009 AT 4:42 PM