Hello, didn't understand on your question what the .ard 57 was. If possible check out the code tester from Auto Zone to check the codes.
There are times that non OEM fuel pumps cause problems. You need to check the fuel pressure. I have attached that. Did you change the fuel filter? If it is restricted the lack of fuel will be a problem.
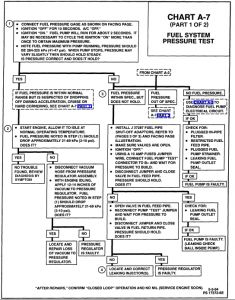
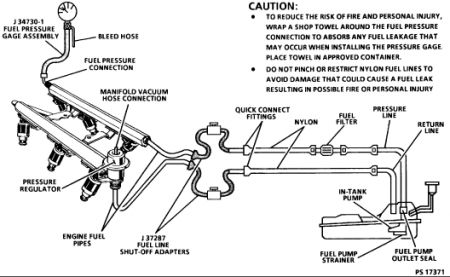
CIRCUIT DESCRIPTION
When the ignition switch is turned "ON," the Powertrain Control Module (PCM) will turn "ON" the in-tank fuel pump. It will remain "ON" as long as the engine is cranking or running, and the PCM is receiving reference pulses. If there are no reference pulses, the PCM will shut "0FF" the fuel pump within 2 seconds after ignition "ON" or the engine stops.
An electric fuel pump, attached to the fuel sender assembly (inside the fuel tank), supplies fuel through an in-line filter to the fuel rail assembly. The pump is designed to provide sufficient fuel flow for all engine demands. A pressure regulator attached to the fuel rail, keeps fuel available to the injectors at a regulated pressure. Unused fuel is returned to the fuel tank by a separate line.
The fuel pump "test" connector is located on the passenger side of the engine compartment near the relay center.
CHART TEST DESCRIPTION
Number(s) below refer to circled number(s) on the diagnostic chart.
Connect fuel pressure gauge as shown in illustration. Wrap a shop towel around the fuel pressure connection to absorb any small amount of fuel leakage that may occur when installing the gauge. With ignition "ON" and fuel pump running, pressure should be 284-325 kPa (41-47 psi). This pressure is controlled by spring pressure within the regulator assembly.
When the engine is idling, manifold pressure is low (high vacuum) and is applied to the pressure regulator diaphragm. Vacuum will offset spring pressure and result in lower fuel pressure. Fuel pressure at idle will vary somewhat depending on barometric pressure but, should be less than pressure noted in Step (1).
A system that does not hold pressure is caused by one of the following:
Leaking fuel pump check ball.
Leaking fuel pump outlet seal.
Leaking valve/seat within pressure regulator.
Leaking injectors(s).
A leak in injector can best be determined by checking or a fouled or saturated spark plug(s). If a leaking injector can not be determined by a fouled or saturated spark plug, the following procedure should be used:
Remove intake plenum.
Remove fuel rail but leave fuel lines connected.
Lift fuel rail out just enough to leave injector nozzles in the ports.
WARNING: To reduce the risk of fire and personal injury that may result from fuel spray on the engine, make sure fuel rail is positioned over injector ports and injector retaining clips are intact .
Pressurize the fuel system and observe injector nozzles.
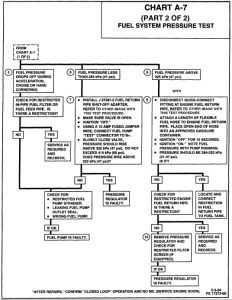
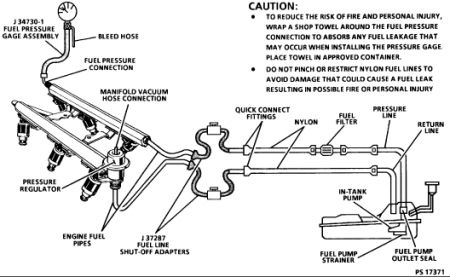
CHART TEST DESCRIPTION
Number(s) below refer to circled number(s) on the diagnostic chart.
Fuel pressure that drops off during acceleration, cruise or hard cornering may cause a lean condition and result in a loss of power, surging or misfire. This condition can be diagnosed using a Tech 1 scan tool. If the fuel system is very lean, the HO2S will stop toggling and output voltage will drop below 500 mV. Also, injector pulse width will increase. NOTICE Make sure system is not operating at "Fuel-Cut off" which may cause false readings on the scan tool.
Fuel pressure below 284 kPa (41 psi) may cause a lean condition and may set a Diagnostic Trouble Code (DTC) P0131. Driveability conditions can include hard starting cold, hesitation, poor driveability, lack of power, surging or misfire.
Restricting fuel flow in the fuel return line as directed causes fuel pressure to build above regulated pressure. With battery voltage applied to the pump "test" connector, pressure should rise above 325 kPa (47 psi) as the valve in the return line is partially closed. CAUTION: Do not allow pressure to exceed 414 kPa (60 psi) as damage to the regulator may result.
Fuel pressure above 325 kPa (47 psi) may cause a rich condition and may set a DTC P0132. A driveability condition can include hard starting (followed by black smoke) and a strong sulphur smell in the exhaust.
This test determines if the high fuel pressure is due to a restricted fuel return line or a faulty fuel pressure regulator.
The pressure regulator filter screen is designed to trap any contaminants introduced during engine assembly. If dirty, it can be removed with a small pick and discarded without potential harm to the regulator.
Fuel System Pressure Relief Procedures
WARNING:
To reduce the risk of fire and personal injury, it is necessary to relieve fuel system pressure before disconnecting fuel line fittings.
After relieving system pressure, a small amount of fuel may be released when disconnecting fuel line fittings. In order to reduce the chance of personal injury, cover fuel line fittings with a shop towel before disconnecting, to catch any fuel that may leak out. Place the towel in an approved container when disconnect is completed .
FUEL SYSTEM PRESSURE RELIEF PROCEDURE
Tool Required: J 34730-1 Fuel Pressure gauge.
Ignition "OFF."
Disconnect negative battery cable to avoid possible fuel discharge if an accidental attempt is made to start the engine.
Loosen fuel filler cap to relieve tank vapor pressure.
Connect gauge J 34730-1 to fuel pressure connection. Wrap a shop towel around fitting while connecting gauge to avoid spillage.
Install bleed hose into an approved container and open valve to bleed system pressure. Fuel line fittings are now safe for servicing.
Drain any fuel remaining in gauge into an approved gasoline container.
Perform service required.
Tighten fuel filler cap.
Ignition "OFF."
Connect negative battery cable.
Cycle ignition "ON" and "OFF" twice, waiting ten seconds between cycles, then check for fuel leaks. After Repairs, Confirm "Closed Loop" Operation And no Malfunction Indicator Lamp (MIL) (SERVICE ENGINE SOON).
Information on your fuel pump relay
When the ignition switch is turned to the "ON" position (before engaging starter), the energizes the fuel pump relay for two seconds causing the fuel pump to pressurize the fuel system. If the Powertrain Control Module (PCM) does not receive ignition reference pulses (engine cranking or running) within two seconds, it shuts "OFF" the fuel pump relay, causing the fuel pump to stop.
As a backup system to the fuel pump relay the fuel pump also can be energized by the fuel pump switch and engine oil pressure sensor. The sensor has two internal circuits. One operates the oil pressure indicator or gauge on the instrument cluster, and the other is a normally open switch which closes when oil pressure reaches about 28 kPa (4 psi). If the fuel pump relay fails, the fuel pump and engine oil pressure indicator switch runs the fuel pump.
An inoperative fuel pump relay can result in long cranking times, particularly if the engine is cold. The fuel pump switch and engine oil pressure indicator switch energizes the fuel pump as soon as oil pressure reaches about 28 kPa (4 psi).
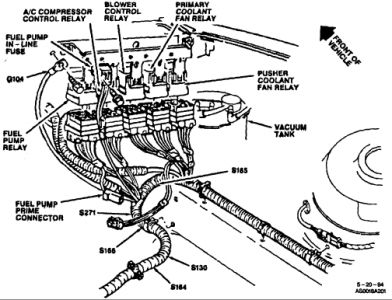
Did you put a new strainer on when you changed the pump?
Last - the fuel pressure regulator
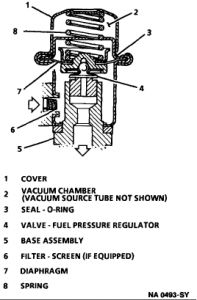
GENERAL DESCRIPTION
The fuel pressure regulator is a diaphragm-operated relief valve with fuel pump pressure on one side, and regulator spring pressure and intake manifold vacuum on the other. The function of the regulator is to maintain a constant pressure across the injectors at all times. The pressure regulator compensates for engine load by increasing fuel pressure as engine vacuum drops.
OPERATION
With the ignition "ON" and engine "OFF" (zero vacuum), fuel pressure at the pressure connection should be 284-325 kPa (41-47 psi). If the pressure is too low, poor performance and a Diagnostic Trouble Code (DTC) P0131 could result. If the pressure is too high, excessive odor and / or DTC P0132 may result.
Hope this helps. Thanks and have a great day!
SPONSORED LINKS
Sunday, October 12th, 2008 AT 12:00 AM