Fuel Pressure Regulators
An essential part of the Fuel System, the Fuel Pressure Regulators' sole purpose is to maintain fuel pressure at a constant differential to manifold vacuum under all engine load conditions. The fuel pressure regulator is responsible for controlling the set fuel pressure of the system.
On returnless fuel systems (RLFS), the pressure regulator is part of the in tank unit installed in the fuel tank. The fuel rail pressure is maintained at a constant level with reference to the surrounding pressure. This means that the difference between the fuel rail pressure and manifold pressure is not constant and must be taken into account when the injection duration is calculated.
The fuel pressure regulator (Fig.1) is of the diaphragm controlled overflow type. A rubber fabric diaphragm (4) divides the pressure regulator into a fuel chamber and a spring chamber. Through a valve holder (3) intergrated in the diaphragm, the spring (2) forces a moveable valve plate against the valve seat so that the valve closes. As soon as the pressure applied to the diaphragm by the fuel exceeds the spring force, the valve opens again and permits just enough fuel to flow back to the fuel tank that equilibrium of forces is achieved again at the diaphragm.
Bosch fuel pressure regulators are competitively priced and sold through leading automotive part stockists. Please see our " �Dealer Locator' at the top of the page to locate you local store
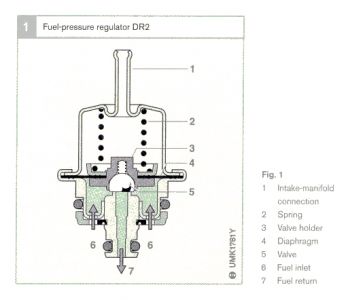
Manifold vacuum, or engine vacuum in an internal combustion engine is the difference in air pressure between the engine's intake manifold and Earth's atmosphere.
Manifold vacuum is an effect of a piston's movement on the induction stroke and the choked flow through a throttle in the intake manifold of an engine. It is a measure of the amount of restriction of airflow through the engine, and hence of the unused power capacity in the engine. In some engines, the manifold vacuum is also used as an auxiliary power source to drive engine accessories. Manifold vacuum should not be confused with venturi vacuum, which is an effect that is exploited in carburetors to achieve a fixed mix ratio between fuel and air.
The rate of airflow through an internal combustion engine is an important factor determining the amount of power the engine generates. Most engines are controlled by limiting that flow with a throttle that restricts intake airflow. Manifold vacuum is present in all naturally-aspirated engines that use throttles (including carbureted and fuel injected gasoline engines using the otto cycle or the two-stroke cycle; diesel engines do not have throttle plates).
The mass flow through the engine is determined by the rotation rate of the engine, multiplied by the displacement of the engine, and the density of the intake stream in the intake manifold. In most applications the rotation rate is set by the application (road speed in a car or machinery speed in other applications). The displacement is dependent on the engine geometry, which is generally not adjustable while the engine is in use (although a handful of models do have this feature, see variable displacement). Restricting the input flow reduces the density (and hence pressure) in the intake manifold, reducing the amount of power that is produced. It is also a major source of engine drag (see compression braking), as the engine must pump material from the low-pressure intake manifold into the exhaust manifold (at ambient atmospheric pressure).
When the throttle is opened (in a car, the accelerator pedal is depressed), ambient air is free to fill the intake manifold, increasing the pressure (filling the vacuum). A carburetor or fuel injection system adds fuel to the airflow in the correct proportion, providing energy to the engine. When the throttle is opened all the way, the engine's air induction system is exposed to full atmospheric pressure, and maximum airflow through the engine is achieved. In a "naturally-aspirated" engine, total engine output is thus determined by the ambient barometric pressure. Superchargers and turbochargers can "boost" manifold pressure to above atmospheric pressure.
Engines with fuel injection have a MAP sensor which measures the manifold absolute pressure to control fuel flow.
Manifold vacuum is caused by a different effect than venturi vacuum, which is present inside carburetors. Venturi vacuum is caused by the venturi effect and depends on the total mass flow through the carburetor. In engines that use carburetors, venturi vacuum is proportional to the total mass flow through the engine (and hence the total power output).
Manifold vacuum may also be "ported" where the opening is placed so it is normally above the throttle plate at idle, but as the butterfly valve opens, the opening is effectively below it, and the opening sees nearly the full manifold vacuum. Ported vacuum is often used for distributors and emissions items.
Most automobiles use four-stroke Otto cycle engines with multiple cylinders attached to a single intake manifold. During the induction stroke, the piston descends in the cylinder and the intake valve is open. As the piston descends it effectively increases the volume in the cylinder above it, setting up low pressure. This sucks in air through the intake manifold and carburetor or fuel injection system, where it is mixed with fuel. Because multiple cylinders suck on the manifold at different times in the engine cycle, there is almost constant suction through the inlet manifold from carburetor to engine.
To control the amount of fuel/air mix entering the engine, a simple butterfly valve (the throttle) is generally fitted at the start of the intake manifold (just below the carburetor in carbureted engines). The butterfly valve is simply a circular disc fitted on a spindle, fitting inside the pipe work. It is connected to the accelerator pedal of the car, and is set to be fully open when the pedal is fully depressed and fully closed when the pedal is released. The butterfly valve often contains a small "idle cutout", a hole that allows small amounts of fuel/air mixture into the engine even when the valve is fully closed.
If the engine is operating under light or no load and low throttle, there is high manifold vacuum. As the throttle is opened, the engine speed increases rapidly. The engine speed is limited only by the amount of fuel/air mixture that is available in the manifold. Under full throttle and light load, other effects (such as valve float, turbulence in the cylinders, or ignition timing) limit engine speed so that the manifold pressure can increase -- but in practice, parasitic drag on the internal walls of the manifold, plus the restrictive nature of the venturi at the heart of the carburetor, means that a low pressure will always be set up as the engine's internal volume exceeds the amount of the air the manifold is capable of delivering.
If the engine is operating under heavy load at wide throttle openings (such as accelerating from a stop or pulling the car up a hill) then engine speed is limited by the load and minimal vacuum will be created. Engine speed is low but the butterfly valve is fully open. Since the pistons are descending more slowly than under no load, the pressure differences are less marked and parasitic drag in the induction system is negligible. The engine pulls air into the cylinders at the full ambient pressure.
More vacuum is created in some situations. On deceleration or when descending a hill, the throttle will be closed and a low gear selected to control speed. The engine will be rotating fast because the road wheels and transmission are moving quickly, but the butterfly valve will be fully closed. The flow of air through the engine is strongly restricted by the throttle, producing a strong vacuum on the engine side of the butterfly valve which will tend to limit the speed of the engine. This phenomenon, known as compression braking, is often used in engine braking to prevent acceleration or even to slow down with minimal or no brake usage (as when descending a long or steep hill). Note that although "compression braking" and "engine braking" are sometimes used to describe the same thing, "compression braking" here refers to the phenomenon itself while "engine braking" refers to the driver's usage of the phenomenon. Compression braking can be greatly increased by opening the cylinders to the exhaust with a valve on downstroke while in overrun, which is often done on large trucks.
Mark (mhpautos.
Information gathered from several web technical sites.
Tuesday, November 17th, 2009 AT 9:55 PM